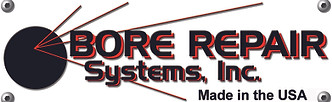
BORE WELDER & LINE BORING MACHINE SPECIALISTS
USA/Canada (800) 650-1005 International: (603) 835-2409
Help me decide on the right bore repair machinery
​
1. Do you only need to weld up bores? (if yes, see "Bore welding equipment" below)
2. Do you only need to machine bores? (if yes, see "Bore machining equipment" below)
3. Do you need to weld up worn bores and then machine them back out? (if yes, see "Complete systems" below)
​
For welding up bores from:
-
.8"-14" (20-356mm) choose a BOA-408i S1
-
.8"-21" (20-533mm) choose a BOA-408i S2
-
.8"-31" (20-914mm) choose a BOA-408i S3
-
.8"-48" (20-1.2m) choose a BOA-408i S4
-
.8"-48" (20-1.2m) with long stroke choose BOA-408i S5
Bore welding equipment
Bore machining equipment
​
For machining bores from:
-
1.9"-11" (48-280mm) choose a C-45 standard
-
1.4"-11" (36-280mm) choose a C-45 with small bar option
-
1.0"-11" (25-280mm) choose a C-45 with small & micro bar option
-
1.4"-14" (36-356mm) choose a C-45 with small option and large bore kit
-
1.4"-24" (36-610mm) choose a BB6 (this kit uses a 2.25" dia main bar - electric or hydraulic) or choose the
-
(for smaller jobs, try the Economical, end-drive style Q150L up to 5")
​
For welding up and machining bores from:
-
1.9"-11" (48-280mm) choose a BRS-2c package
-
1.4"-11" (36-280mm) choose a BRS-3c package
-
1.0"-11" (25-280mm) choose a BRS4c package
-
1.4"-14" (36-356mm) choose a BRS5c package
-
1.4"-24" (36-610mm) choose a BRS6 package
Complete systems with Bore machining system & BOA bore welding system
Now call us at 800-650-1005 or your local Bore Repair Systems agent to get your price!
Have you decided on the system that will work for you? We offer several convenient ways to get your system:
1.) Credit card*
2.) Company check
3.) Bank check
4.) Direct bank wire transfer
5.) Lease purchase
6.) Rental/Try before you buy program.
For options 1-4 please email our sales staff from our "Contact" page or send mail to: sales@borerepair.com. We are available by phone M-F 9am-5pm eastern time, and by fax 24/7.
If you would like to take advantage of our popular "Lease to own" program, simply apply below. Approvals once complete (generally within 2 hours) will be valid for 30 days. Call with any questions 603-835-2409.
*credit card purchases over $1000.00 are subject to a 3% card fee
The finer points of bore repair -
common questions & answers:
Q: I don't understand the pass-though drive system on your bore welder, and why it is so important.
A: The pass-through drive system featured on the multi-patented and patent-pending BOA bore welder means that the bore welder drive can be easily centered (independent of the entire welding gun assembly) by using traditional boring bar centering methods. That is to say you may center the bore welder using a simple 1.25" diameter boring bar or tube, and cones. Also, by having this type of drive system, you may actually mount the drive between two distant but inline bores and weld each side without having to ever reposition the drive! The entire welding gun and extension assembly is simply pulled out of the drive, inverted, and telescoped as needed. Old-fashioned systems do not offer such flexibility, and actually require you to assemble the welding guns and extension shafts and re-feed the welding wire nearly every time you make a bore to bore transition.
Q: I already own a boring bar, or am ordering a boring bar from another manufacturer, will your BOA-408i or BOA-M1 series bore welder be compatible?
A: Yes. Bore Repair Systems, Inc. manufactures and stocks a wide array of precision bore welder to boring bar bearing interface kits for nearly any boring bar.
Q: Spiral versus non spiral feeding, which one is better and why.
A: The BOA-M1 and BOA-408i S1-S5 machines employ a reliable, spiral feed technology, while the BOA-550HD series machines employ a reliable MECHANICAL variable feed.
AGAIN, PUT ANOTHER WAY, NEITHER THE BOA-408i , BOA-M1 series bore welders nor the BOA-550HD series bore welders employ the trouble-prone ELECTRICAL "STEP" FEED.
The BOA-408i series machine is the bore welder of choice for anyone performing bore repairs on holes up to 48" (1.2m) in diameter. The BOA-550HD is a top choice for ultra-long duration, high amp welding jobs in bores typically from 4" (102mm) to 50"+ (1.3m+) Typical users are repairing earth moving machinery, and must have reliable weld bead placement EVERY TIME, with no variations such as those that occur with unreliable ELECTRICAL STEP bore welders. Weld bead placement, if not consistent, results in improper bead to bead and/or bead to base material fusion. Simply put, if this occurs, you must start the job all over again. NOW, what causes ELECTRICAL STEP bore welders to vary their bead placement and "UNDER STEP?"
1.) Incoming voltage variations (using the bore welder in a shop with 120 or 240vac then going to the field and using the bore welder on a engine drive power supply with 120 or 240vac output)
2.) A dirty or dusty feed quill on the bore welder (increased feed resistance)
3.) A control panel that is out of calibration (happens over time with no warnings). or
4) A worn out and/or binding axial feed motor gear train.
NOW, when the bore welder provides an UNDER STEP situation, the unfortunate operator will not recognize this until after carefully welding up the bore/s, removing the bore welder, hooking up the boring unit, then cutting the bore welds to size the bore. Users report (and we have seen ourselves) large sections of the apparently fine welded bore (beads) come out, like a soup can, as they are not fused (did not penetrate) into the base material. Again, this happens because the machine did not step (travel) enough, therefore it stacks the weld beads too tightly so they only really fused to prior weld beads and not the base material of the bore. At this point you must entirely machine the remaining weld out of the bore, and start all over. NOW, OVER STEPPING, is typically caused by
1.) Control box feed circuitry out of calibration or
2.) Incoming voltage that is higher than the voltage where the control box was originally calibrated. or
3.) worn-out feed geartrain.
The worst thing about this unnecessary complexity is that the operator has NO WAY of knowing day to day, job to job when or if the ELECTRICAL STEPPING bore welder system is going to act up and step an amount different than he has set on the control box panel. Not exactly a good feeling. Again, the BOA-408i, with its far simpler spiral drive will provide exactly the same feed rate EVERY TIME, case closed. Every revolution of the welding head on a BOA-408i will result in the optimum .125" feed rate, guaranteeing every bead of weld will be deposited in the perfect location half on the previous bead and half on the base metal. In other words, properly TIED IN. A variable step is completely unnecessary in nearly every bore repair for heavy equipment bores up to 24" diameter, and rarely even desirable for bores up to 50" diameter. The Bore Repair Systems, Inc. BOA-550HD does offer a mechanically adjustable feed rate, as it is the bore welder of choice for larger dissimilar-material cladding operations on very large diameter bores...and in certain HD (heavy duty) applications a very heavy buildup is required, making it desirable to mechanically vary the feed rate. The BOA-550HD's mechanical adjustable cam feed is immune to the voltage and calibration issues that plague old-tech electrical feed bore welders. Bore Repair Systems, Inc. patented and EURO CE Compliant bore welders are built tough and reliable for a world market. BOA bore welders do not require nor do they have the sensitive, unreliable electrical and mechanical assemblies seen on variable-step electrical feed borewelders. BOA-408i, BOA-M1 and BOA-550HD therefore are far better suited to provide long-term consistent service in the real world rough environments. You will not face expensive, time consuming annual rebuilds with our bore welding systems once the warranty has expired.
Q: If the BOA bore welders are best, why are they priced so reasonably?
A: Since 1995, Bore Repair Systems, Inc.,a family owned and operated company, has been committed to providing the finest quality, easiest to use bore welders, boring bars and bore sizers to the public at the lowest possible prices. The elegantly simple, reliable BOA bore welders have been awarded numerous patents, are proudly manufactured in the United States, and have passed European Standards quality and safety (CE) testing. AS noted above, BOA bore welders do the job without unnecessary, unreliable and costly complexity, and we pass on the savings to you. The BOA is a bore welder that was designed with logic, by engineers that spend time in the field performing bore repairs. By viewing the machine, it is immediately apparent how it works. This logical design means it will be used , and does not require any special training or staff to operate.
Q: Can you explain why the "dual tool ports" you have in your boring bars are better than traditional single tool port boring bars?
A: Dual tool port bars are a huge time saver when used in conjunction with our popular ID bore measuring snap gage system and micrometer tool bit adjustment system. With the dual port design, you simply place your cutting bit in the rear port (the tool port that enters the bore last), cut your bore, advance back to your start position then slip in your compressed ID snap gage into the port directly in front of the tool bit. You then simply feed your bar so that snap gage is in the bore 1/2 inch and take your bore diameter reading. Yes, this means you no longer have to remove your tool bit to make a bore measurement. This means your tool bit baseline location is not disturbed. With the snap gage reading, you then simply attach the micrometer tool bit adjuster, loosen tool retainer screw and retract bit the desired amount to take your final sizing cut. But wait, it gets better. Once you re-tighten the tool bit retaining screw and remove your tool adjuster, you then begin your final cut. Stop about 1/4-1/2" in, retract cutting bit once again (but leave it in the tool port), and quickly re-check the bore with the snap gage to make sure your bore is the perfect size. Doing this final check is possible with the dual port design, saving you from a costly mistakenly over cut situation. Once you confirm bore is perfect you resume cutting and finish the job. Our dual port bar design along with our custom snap gages and tool adjusters give you the proper tools to do the job in the most efficient and accurate manner possible. Recently a Bore Repair Systems, Inc. customer reported another big benefit to the dual-port bars that he utilizes. He indicated that it is very handy to place one cutter in the front tool port (for the rough cut through the bore) and a second cutter in the rear tool port (set for the final cut diameter). This allows him to complete the bore repair with just one stroke through.
Q: Can you explain your BRS system exclusive "tunable" bearing system and why it is better than other boring bar systems?
A: The exclusive Bore Repair Systems, Inc. "tuneable" bar support bearing system is simply the best when it comes to precision cutting. Using a specially designed bearing support housing, users of the new C45, BB and AM boring bar system are able to actually "tune" their bearings. This means, unlike other boring bar systems which offer a traditional roller bearing support, we use a special standard bearing which resides in a housing which may be tightened to eliminate all of the play (gap) between the boring bar outside diameter and the bearing inside diameter. While old fashioned boring systems typically suffer from excessive play (from .003-.006") in this area, Bore Repair Systems, Inc. boring bar bearings can be tuned or "tightened" to .0001". You can imagine how important this is if you are repairing a machine bore and want to be able to repair to a tight .001" tolerance.
Q: I have heard that Bore Repair Systems, Inc. boring bar systems can actually be used as portable drill presses and are excellent at dealing with blind bore machining as well. Can you explain?
A: Bore Repair Systems, Inc. has developed a unique precision "joinable" bar support system which allows the boring bar system to be used for blind hole boring. (boring into a bore where there is no way to attach a second bar support) The Bore Repair Systems, Inc. design couples two supports together, back to back providing one, very rigid support. The outermost support holds the boring bar drive and the innnermost contains the bearing. This setup, in conjunction with the cutting bit inserted into the bar end cutter port allows for a blind bore cut. To use the Bore Repair Systems, Inc. boring bar drive as a drill press, the bearings again are joined, and the optional morse tapered bar is used. Depending on the bar diameter, the morse taper is either a #3 or a #4. This morse taper allows you to insert a mating male morse tapered end drill or a chuck with morse adapter.
-
Use a good quality wire with a large "cast". Check cast by pulling off 5 or 6 feet of wire, drop it on a hard floor, and measure the resulting diameter. If it is 48" or greater, you have a desirable cast wire...if diameter is under 48" you may experience slight weld bead instability. TRY OUR OWN 70S6 SOLID ULTRA LARGE CAST WIRE AVAILABLE IN .030" and .035". You'll Love It! For .030" order part no. 1103, for .035" order part no. 1202
-
For steel welding we recommend a gas shield mixture of Argon and CO2. Percentage of Argon minimum:75%, maximum: 92% flowrate varies but indoors generally 25--30 cfh is sufficient. Outdoor welding may require that you cap the end of your bore with tin foil, this will help contain shielding gas if windy.
-
Use a power supply that allows voltage adjustment while you are welding. Click-type voltage adjusters do not allow fine adjustment once your bore welder has started.
-
For skip welds or bores where you only need to build up a portion of the bore, we recommend hooking your BOA up to a wirefeeder that has a burnback control installed.
-
Set torch nozzle stick-out at about 1/8" from workpiece bore.
-
Use proper torch rotation speed. Measure bore you will be welding in and refer to chart on borewelder for approximate speed setting. To vary buildup thickness you may adjust rotation speed and/or wire feed rate.
TIME REQUIRED FOR BORE BUILDUP
(helpful when estimating job times)
Metric: Calculate by multiplying the diameter (mm) by the length (mm) by .002
Example: Diameter of the bore= 65mm; Length of the bore= 110mm
Normal build up time=65 x 110 x .002 =14.3 minutes
English: Calculate by multiplying the diameter (in.) by the length (in.) by 1.25
Example: Diameter of the bore= 4.2 inches; Length of the bore= 3.6 inches
Normal build up time=4.2 x 3.6 x 1.25 =18.9 minutes
WIRE DEPOSITION RATE
(useful when calculating anticipated wire usage)
Metric: Calculate by multiplying the following:
For .8mm wire- multiply the wire feed speed in mm/min by .00022
For .9mm wire- multiply the wire feed speed in mm/min by .00033
For 1.2mm wire- multiply the wire feed speed in mm/min by .00050
Example: Wirefeed rate= 7400mm/min; wire size= .8mm
Deposition rate= 7400 x .00022 = 1.63 kg/hr.
English: Calculate by multiplying the following:
For .030 in. wire- multiply the wire feed speed in in./min by .0123
For .035 in. wire- multiply the wire feed speed in in./min by .0167
For .045 in wire- multiply the wire feed speed in in./min by .0277
Example: Wirefeed rate= 320 in./min; wire size= .030 in.
Deposition rate= 320 x .0123 = 3.94 lb./hr
THE BOA-408i, BOA-M1 AND BOA-550HD SERIES BORE WELDERS....DESIGNED SPECIFICALLY FOR WORKING ON
HEAVY EQUIPMENT BORES. TAKE ADVANTAGE OF THE BOA-408i FREE TRIAL PROGRAM TODAY.
BELOW NOTE THE UNIQUE PASS-THROUGH DRIVE DESIGN OF THE BOA-408i PORTABLE BORE WELDER.
THIS FEATURE, WHEN COUPLED WITH THE BOA REVERSIBLE, TELESCOPING TORCH EXTENSION MAKES
THE BOA PERFECTLY SUITED FOR REPAIRING CONSTRUCTION AND MINING EQUIPMENT BORES. ALSO
SHOWN IS THE OPTIONAL CENTERING CONE AND ROD KIT USED TO CENTER THE BORE WELDER THE
SAME WAY A BORING BAR MAY BE CENTERED. AS A BONUS, IF YOU ARE ALREADY USING A BORING
BAR SYSTEM THAT UTILIZES 32MM (1.25") BARS, YOU MAY ACTUALLY CENTER THE BORE WELDER DRIVE USING
YOUR EXISTING BAR.